The fire of a large bakery plant in Ostrava at the end of last September was literally a textbook example of the behaviour of large steel structures built to the statutory fire resistance ratings. One of the walls deflected during the fire, so a structural engineer was called in to the site and he ordered that the embedded concrete structure in a part of the hall be torn down.
A half of the flat roof with a size of 70 × 40 metres was on fire. Firemen got the fire under control in less than two hours using high rise equipment, and final extinction took several more dozen minutes.
The production hall is quite large. It consists of the feedstock buildings, the single-nave production hall with a central pillar, an office building with employee cloakrooms and a dispatch building. The hall was in operation from 2008. It is a LLENTAB assembled steel hall encased in a combination of two ventilated façades. The roof included several roof lights and held quite a lot of ventilation equipment. Considering its purpose the hall was not complex in fire fighting terms.
Fire protection concept
A standard LLENTAB solution was used for fire protection in accordance with fire protection design of the project. The required fire resistance rating of vertical supporting steel structures was R 15 with KNAUF protection system – RED plaster boards 12.5mm thick with an actual fire resistance rating of R30, with steel sheet casing protecting it form damage during normal operation. There was no fire resistance specification for the supporting steel truss structure of the roof. The ceiling in the office part was secured with a fire-proof plasterboard soffit. The perimeter walls of the hall were designed with a EW 30 DP1 fire resistance rating to stop the spread of fire outside. This is insulated 4F/4FI type wall cladding with the actual fire protection rating of EW 90 DP1 with the outer layer made of ventilated façade using Cetris cement bonded particle boards or DEKLAMELA metal façade blades. Thermal insulation used ROCKWOOL boards made of basalt wool.
Course of the fire
According to the preliminary investigation reports, the fire started with the explosion of a boiler in the oil management area in the main part of the production hall. From there, it propagated through the roof structure filling. Considering all circumstances, it can be said that the steel hall structure behaved in an ideal manner despite the minimum requirements for fire protection and did not degrade or collapse.
Restoration
The hall’s supporting structure remained and could be restored once decontaminated. The hall restoration work started in mid-November last year and finished mid-April this year.
Hall cladding immediately after the fire.
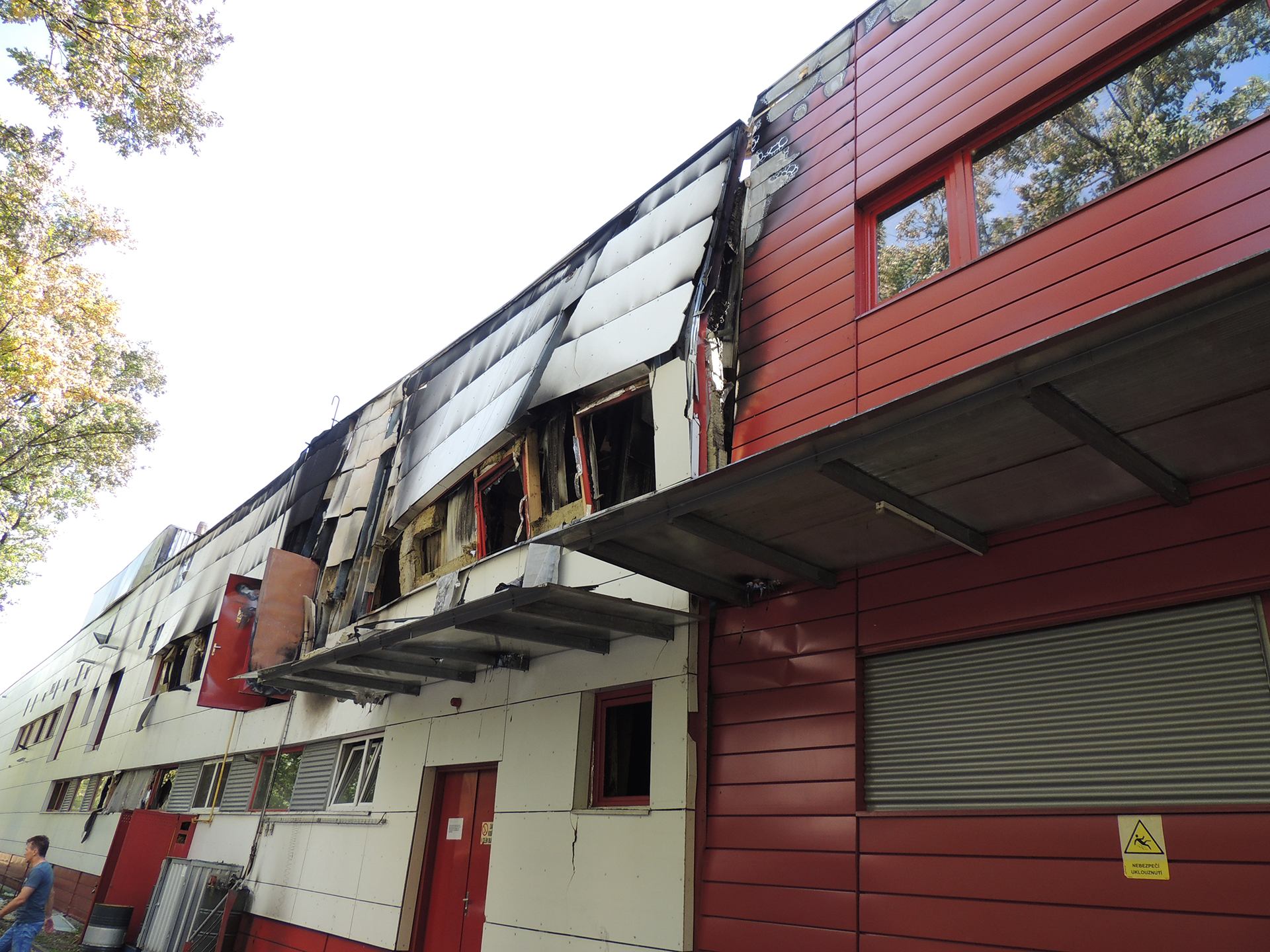
Close-up of truss girders after the fire.
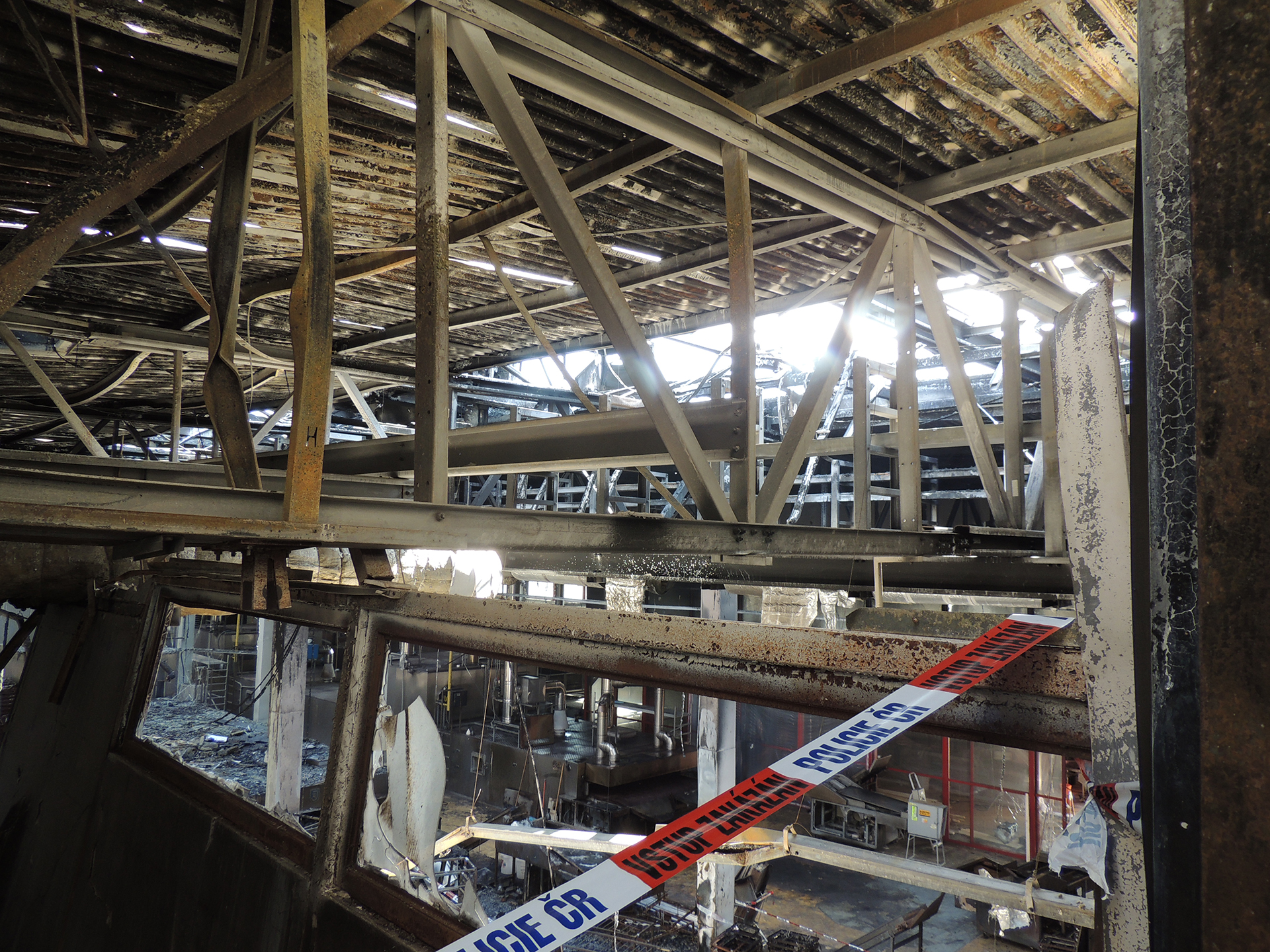
We originally considered simplification from the initial hall concept. For example, we wanted to replace the original composite façade with sandwich panels to accelerate the restoration. We eventually stuck to the original design since the façade restoration was not overall and it was connected to the existing cladding. Having agreed with the investor we just improved the roof structure, replacing the former filling with 60 mm thick basalt wool with non-flammable and 60 mm thick self-extinguishing polyurethane boards.
We have been collaborating with LLENTAB for almost twenty years. Our cooperation started with a hall project here in Ostrava-Martinov and continued on the sites for other HRUŠKA plants. As any budding Czech business, we were looking for a truly affordable and efficient solution that would help us go forward. We have no negative experience with LLENTAB throughout our cooperation. They have always been helpful to the maximum. For example, their people arrived within twenty-four hours after the evening fire of our plant. They ascertained the scope of damage, contacted a structural engineer and proposed a solution for the repair. Of course, the availability of the hall’s production documents was a benefit. As a result, they could immediately commission the production of the damaged segments that had to be replaced in Sweden. Even though autumn is a very busy period for the construction industry, they did their best and reassigned some of their resources to restore our hall. This minimised our lost profit, since the really quick restoration allowed us to slowly ramp-up trial operation after about seven months. We used above-standard fire protection of the roof structure in the restored hall and we will do the same in our future projects. We are considering building a back-up bakery plant in a matter of years, which would allow us to continue production in the event of maintenance or failure of the main production line. We will certainly use LLENTAB’s steel hall system for this project.
Production part of the hall after the restoration.
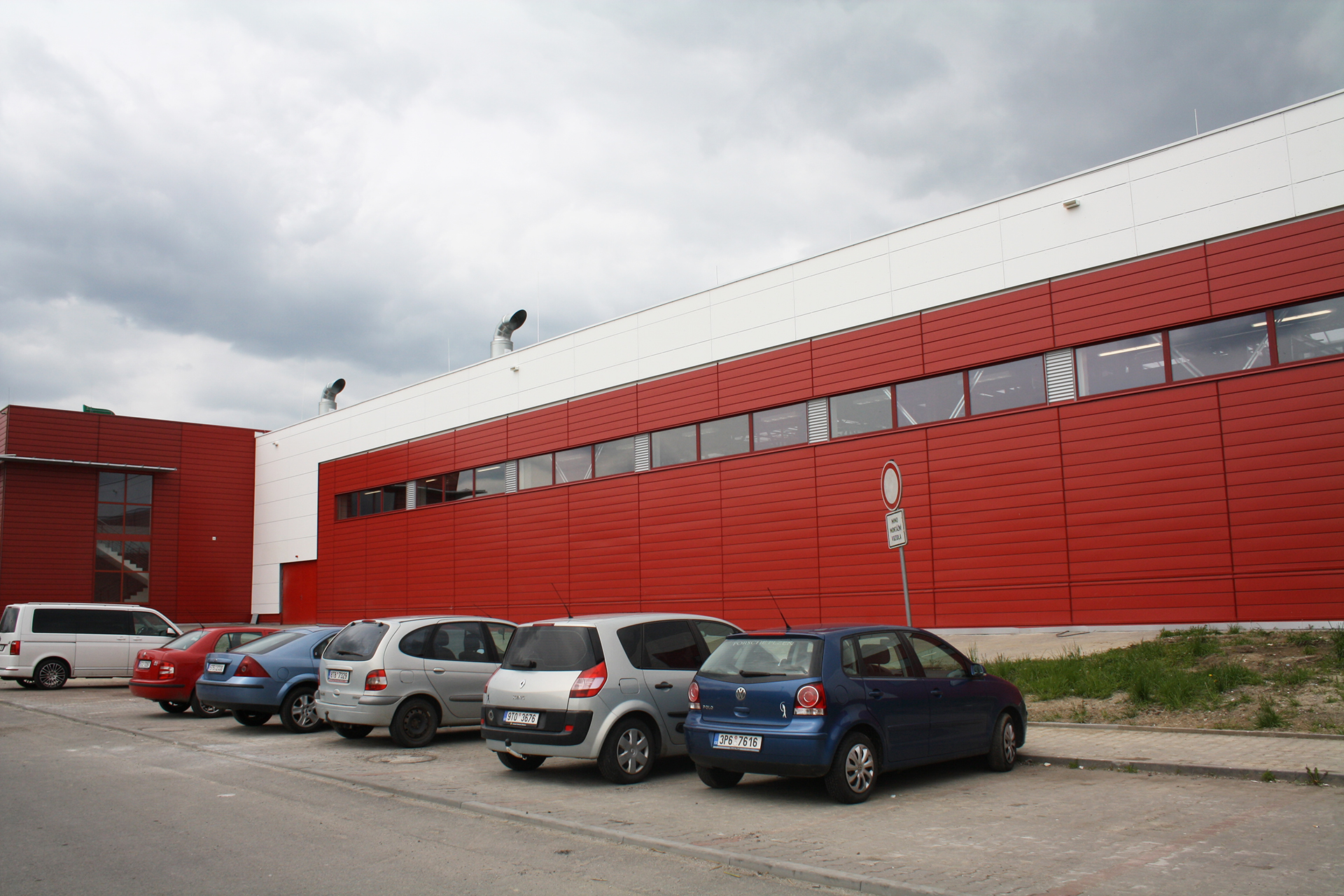